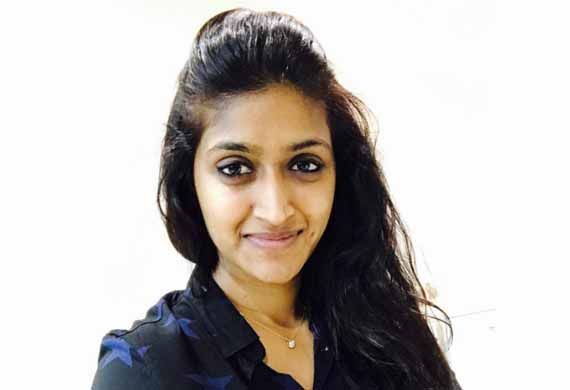
IoT & Connected Machines Transforming Textile Manufacturing Industry
By: Karunya Sampath, Co-Founder & CEO, Payoda
Karunya Sampath, a tech leader with extensive Wall Street experience, combines a software engineering background with a passion for spirituality. Dedicated to mentoring and personal growth, she leads an active lifestyle while exploring deeper spiritual practices.
Technological advancements are reshaping industries across the globe. With the advent of Industry 4.0, the integration of the Internet of Things (IoT) and connected machines is revolutionizing the way textiles are produced, paving the way for enhanced efficiency, productivity, and sustainability.
IoT is a network of interconnected devices embedded with sensors and software that collect, exchange, and analyze data in real time. In textile manufacturing, IoT is heralding a new era of intelligent production processes, where every stage - from fiber production to finished fabric - is infused with intelligence.
How are IoT and Connected Machines Paving their Way in Textile Manufacturing?
Predictive Maintenance for Seamless Operations
One of the critical applications of IoT in textile manufacturing is predictive maintenance. Traditionally, machine downtime due to equipment failures could disrupt production schedules and incur significant costs. However, with IoT-enabled sensors monitoring equipment performance in real-time, potential issues can be identified proactively. By analyzing data on machine health and performance, manufacturers can schedule maintenance tasks strategically, minimizing downtime and maximizing operational efficiency.
Energy Efficiency for Sustainable Operations
In an era where sustainability is paramount, IoT offers textile manufacturers a powerful tool for managing energy consumption and reducing environmental impact. By deploying smart meters and sensors, manufacturers can monitor gas, electricity, and water usage in real-time. This data enables them to identify inefficiencies, optimize energy usage, and meet sustainability goals. Moreover, IoT-driven insights empower manufacturers to make informed decisions about resource allocation, driving towards a more sustainable future.
Ensuring Safe Work Environments
Worker safety is a top priority in any manufacturing setting. IoT plays a crucial role in creating safer work environments in textile factories. Environmental sensors monitor air quality, temperature, and humidity levels in real-time, ensuring that conditions remain within safe limits for employees. Additionally, predictive maintenance helps prevent accidents caused by equipment malfunctions, further enhancing workplace safety.
Nanotechnology: A Game-Changer in Textile Production
In addition to IoT, nanotechnology is emerging as a game-changer in textile production, offering innovative solutions for creating durable, sustainable fabrics. By manipulating nanoparticles, manufacturers can enhance textile properties such as water repellency, UV protection, and odor elimination. Nanotechnology holds the promise of revolutionizing the textile industry, enabling the production of high-performance fabrics that meet the evolving demands of consumers and the environment.
Challenges and Considerations
While the potential benefits of IoT and nanotechnology in textile manufacturing are undeniable, there are challenges that manufacturers must navigate. Integration costs, standardization issues, and the complexity of implementing new technologies are among the key considerations. However, with strategic planning, investment in research and development, and a commitment to innovation, textile manufacturers can unlock the full potential of IoT and nanotechnology to drive growth and competitiveness in the Industry 4.0 era.
Final Thoughts
In conclusion, IoT and connected machines are transforming the textile manufacturing industry, ushering in a new era of efficiency, sustainability, and innovation. By harnessing the power of IoT, manufacturers can optimize production processes, reduce costs, and enhance product quality. Meanwhile, advancements in nanotechnology offer exciting possibilities for creating next-generation textiles with unprecedented performance and sustainability attributes. As textile manufacturers embrace these technologies, they position themselves at the forefront of Industry 4.0, poised for success in the rapidly evolving global marketplace.